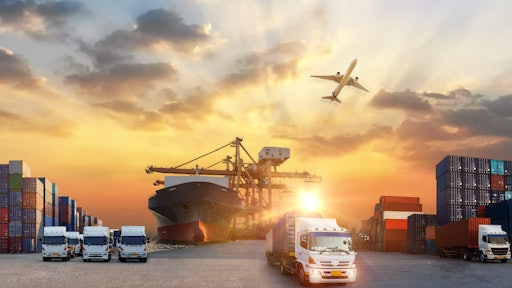
Over the last year, we’ve seen an unprecedented wave of supply chain catastrophes. From a drought at the Panama Canal, to attacks by Houthi militants on commercial vessels in the Red Sea, to a container ship collapsing a 1.6-mile-long bridge – it’s stranger than fiction.
With the rise of globalization, our supply chains are inherently more vulnerable. Suppliers are further away, and that means there are more opportunities for disruptions to arise. But it also means there are more avenues to mitigate risk.
First, some much-needed good news: with the Panama Canal Authority adding daily transit slots in March, it does seem the worst of the Panama Canal drought impacts are over (for now). According to project44’s data, maximum vessel transit time through the canal has come down from its high of about nine days in November and is now just over a day longer than before the drought restrictions began in July 2023. That said, the threat of extreme weather disrupting supply chains is not over. With global climate change, the frequency and severity of droughts is likely to increase. To brace for this new reality, supply chain professionals need to bake climate risk into their planning – accounting for the impacts of both predictable weather patterns like drought exacerbated by El Niño and acute weather events like hurricanes.
Compounding the risks of climate change, there are numerous other factors threatening supply chains: geopolitical events (like the Houthi attacks), increasing labor strife (the number of US labor strikes reached a 23-year high in 2023), economic factors (persistent inflation) and the looming potential for yet another black swan event (like the COVID-19 pandemic). Instability is inevitable so it’s a crucial time to apply lessons learned to build more resilient, High-Velocity supply chain operations.
Here are three pieces of advice I offer supply chain leaders to get ahead of risks:
1. Old-school visibility won’t cut it anymore – focus on inventory in motion. Historically, supply chain visibility was about understanding where goods are and when they’ll arrive at the unit level. With that approach, calculating the impact of a supply chain disruption requires some back-of-the-napkin math – you have to manually pair different vessels to shipments to orders. And building your business’ contingency plan on calculations you don’t have a lot of confidence in is likely to result in costly errors. Inventory-in-motion visibility is both a mindset and a technology shift to better understand the health of your supply chain operations holistically. It’s about viewing all your inventory across the globe together to determine how a disruption will impact inventory and where to reallocate from.
Here's a real-world example: an automotive company typically relies on the Suez Canal as a key shipping lane for its parts. Because of the Houthi attacks in the Red Sea, the company now must reroute around the Cape of Good Hope. If the company only has basic visibility, its team knows that a given shipment will be delayed, but they can’t reliably forecast the impact on their inventory. They don’t know the exact percentage of inventory that’s at rest and whether there’s enough safety stock padded into that specific timeline. So, to play it safe, they pay extra to expedite the shipment via air.
On the flip side, if the automotive company is using inventory visibility, it sees the exact amount of inventory that’s at risk and is going to be 10 days late to areas where the company doesn’t have 10 days of safety stock padded. Based on these insights, one team member (instead of multiple different teams) can evaluate where to redistribute inventory and cut air expedites in half (or more), depending on inventory levels and locations.
In a world where disruption is the only constant, the ability to be agile with inventory planning pays major dividends. Supply chains can be money pits when businesses take a reactive and manual approach to managing them. For industries like automotive that operate on lean, just-in-time models, every hour production is halted due to missing parts amounts to upwards of a million dollars lost. So, proactively investing in better inventory visibility is where you’ll see the biggest return when a crisis arises.
2. The first day of a supply chain crisis is the critical window to respond. When disaster strikes, you can’t afford to spend a week analyzing the impact and determining a path forward. It’s critical to be ready with real-time data and insights to formulate an initial response within the first 24 hours (or less). In the heat of the moment, it’s hard to communicate with carriers, because they’ll also be busy responding to the crisis. For this reason, it’s crucial to proactively increase integration across stakeholders and ensure that, as a shipper or beneficial cargo owner (BCO), you are receiving real-time updates from carriers. There is always a domino effect with supply chains, so the earlier you can intervene in a disruption, the more likely you are to mitigate downstream consequences.
Here's an example: in the wake of the Francis Scott Key Bridge collapse in Baltimore, several carriers invoked the “force majeure” clause. So, if a ship was rerouted to the Port of New York because of the incident, the carrier’s customer would then be responsible for transportation from this new port of discharge to the original destination in Maryland. That means the cost gets passed on to the company – and it can be a hefty bill. Companies must contend with both surging spot rates due to higher demand, and unexpected detention & demurrage fees for containers stuck at ports. With accurate data and real-time visibility at their disposal, shippers can react quickly – locking in competitive spot rates, arranged for freight to be moved via traditional means or expedites, and communicating delays to customers – regardless of how a carrier responds.
3. Rerouting isn’t always a tenable option – so get comfortable operating within constraints. Supply chains have a lot of fail-safes built in. There’s always a way to get something from point A to point B, but there are only a few options to do it in a cost-effective manner. Earlier this year, we faced a conundrum where two of the most efficient supply chain lanes – the Panama Canal and the Suez Canal – were simultaneously restricted. Alternative routes come with costs, and companies only have so much budget to absorb these costs before the overages must be passed down to consumers.
As global trade (and our economy) becomes more volatile, supply chain stakeholders have a responsibility to engage in scenario planning earlier and more often. Sometimes Plan A and Plan B fall through, so take the time to map out a Plan C and prepare for the costs of exercising your last-resort option.
The global disruption wrought by the COVID-19 pandemic was a wake-up call for supply chain professionals. Since the pandemic started over four years ago, we’ve seen massive investment in supply chain operations and measurable improvements in terms of resiliency. Through forced practice, we’ve become better at navigating the fragility of supply chains. And that gives me hope that we as supply chain professionals can tackle whatever curveballs the world throws at us. With the right tools and technology on your side, you can enable your supply chain teams to operate at high velocity when a crisis does come.